Initiatives for Effective Use of Resources Back Number (2011)
Back to Latest Initiatives for Effective Use of Resources
Basic Approach
All of the resources that are indispensible for Minebea Group Products are limited, including such raw materials as steel, resin, and ceramics, energy sources like oil, coal, and natural gas, and even water. Moreover, rare earth elements essential for the production of mobile handsets, PCs, and electric appliances are not only limited in terms of reserves, but are produced in only a few countries, making them likely candidates for export-related and other restrictions.
In addition, the mining of gold, tantalum, tin, and tungsten in the Democratic Republic of Congo and surrounding countries serves as a source of funding for organizations outside the control of government, and large-scale damage to the environment and local ecosystems caused by unrestricted development has become a major problem for international society.
Given the fact that rare earth elements are used in such a wide range of products worldwide, the Minebea Group considers the proper and efficient use of these resources to be an important management objective.
Results of FY2010 Initiatives
In FY2010, principal raw materials used by Minebea Group as a whole included approximately 65,300 tons of steel and 6,900 tons of resin, up approximately 20% over the preceding term due in part to our business recovery.
At the same time, the volume of waste emitted by the Minebea Group outside its facilities and ultimately sent to landfill totaled 4,086 tons, a reduction of approximately 17% compared to FY2009.
Initiatives at Offices
Effective Use of Water Resources (Karuizawa Plant)
Filtration system for effective use of spring water
The Karuizawa Plant, which manufactures such products as bearings for the aviation industry, formerly obtained water for its manufacturing processes from the municipal water supply. Now, however, the plant relies exclusively on water sourced from a spring on the plant's premises. Previously the spring water was simply discharged outside the factory, but switching it to industrial use means more effective water resource use and reduced manufacturing costs. The plant now uses approximately 200 tons of spring water daily.
Conversion of Raw Kitchen Waste into Biogas (Thailand)
Biogas generation plant at Lop Buri Plant, Thailand
Our Bang Pa-in and Lop Buri Plants have constructed biogas generation plants as part of the Thai Ministry of Energy's renewable energy plan. The biogas generated is being used in place of LP gas in the plant cafeteria.
Use of biogas helps reduce the use of fossil fuels, and since only CO2 absorbed during plant and animal growth is released during biogas combustion, the energy released was generated via the life cycle and thus has an extremely low environmental impact.
Recycling of Swarf and Cutting Oil (Bang Pa-in Plant)
Compressed swarf briquettes
To further promote recycling of swarf and cutting oil in our Bang Pa-in Plant in FY2010, we placed additional compression devices in the swarf collection area.
Compressing swarf into briquettes reduces swarf volume and simplifies storage and transport. In addition, the compression process separates residual cutting oil from the swarf, allowing it to be recovered. As a result, less space is needed for swarf storage, and the swarf does not need to be collected for recycling as frequently, which contributes to reduction of transport-generated CO2 emissions.
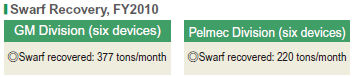
Utilization of Packaging Waste Products Such as Wood Boxes (Thailand)
A sign, tables and chairs made from packaging waste products
The Bang Pa-in and Ayutthaya Plants recycle the wood from wood packing boxes and other forms of packing waste to create signs, tables, shelves, desks, chairs and other useful objects that are used on the plant premises.
Vial Material Recycling (Domestic Distribution Warehouses)
Vials are tubular polyethylene containers used to store anywhere from tens to around a hundred miniature bearings manufactured by Minebea, and are used as packaging to deliver bearings to customers. When delivering ball bearings manufactured in overseas facilities to customers in Japan, empty vials are not returned to their country of original manufacture, but are returned to domestic distribution warehouses where previously they were discarded.
Since the material of the container itself is pure resin, recycling had been under consideration for some time. However, since it was difficult to separate such material as the paper labels affixed to the vials, until now they had been processed as industrial waste (solid fuel combustion). However, advances in technology have made it possible to apply material recycling treatment to these vials, even with paper and other foreign substances adhering, and this allows Minebea Group used vials to also be recovered as a valuable resource.
In FY2010, approximately nine tons of vials were processed into resin pellets, after which they were used to produce such products as planters and flower pots as well as artificial wood with a very similar appearance to natural wood. When other products besides vials that can be recycled are included, such as container cases and trays, the total amount of material recycled from our domestic distribution warehouses totaled approximately 12 tons.
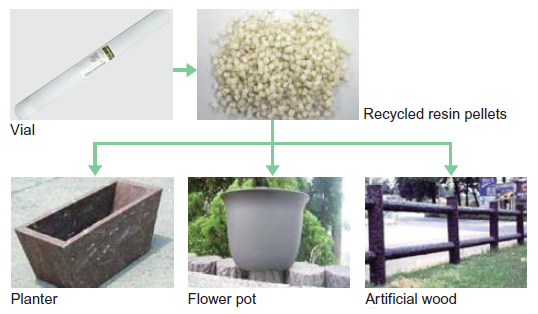
Reducing Waste
Although the Minebea Group makes every effort to reduce the volume of waste it generates through its business activities, at present it is difficult to reduce the amount produced to zero. We work to minimize the volume ultimately sent to landfill by recycling waste as thoroughly as possible through treatment processing.
However, treatment methods vary due to conditions in different countries, although the waste itself is the same. In FY2010, the entire Minebea Group emitted approximately 55,405 tons of waste outside its facilities, of which an estimated 4,086 tons (7.4%) were sent to landfill.
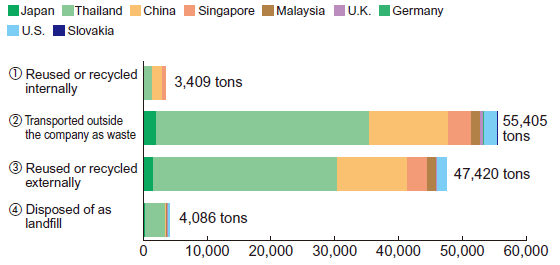