It is a present position.
- Home
- Our Strengths
- Tech Column : Rotation angle sensor (resolver) for EV/HEV drive motor
Main text is as follows.
Mobilization of know-how cultivated over half a century
Realization of the development and mass production of rotation angle sensors supporting the core of the next-generation eco-friendly cars
- Rotary components
Rotation angle sensors (resolvers) for EV/HEV drive motors
Electric vehicles (EVs) have been attracting attention as a type of next-generation eco-cars. With the rise in popularity of hybrid electric vehicles (HEVs), the market is expected to expand. The VR resolver (rotation angle sensor) is a vital component of the motor that plays a key role in EVs. Over the past half a century, MinebeaMitsumi has cultivated electromagnetic and other resolver technologies through the development and production of aircraft sensors, industrial motors and various rotary components. MinebeaMitsumi supports next-generation eco-friendly cars in the VR resolver that directly affects EVs' power consumption rate and driving performance.
Basic mechanism of resolver
A resolver is a type of rotation angle sensor for controlling the drive motor that is the power source of EVs. By efficiently controlling the motor, power consumption can be suppressed. To control the motor according to various driving conditions of a vehicle, it is necessary to detect the magnetic pole position of the motor and accurately grasp its rotational speed. The resolver serves as a sensor for these tasks.
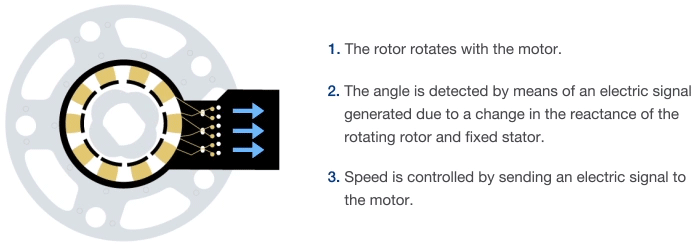
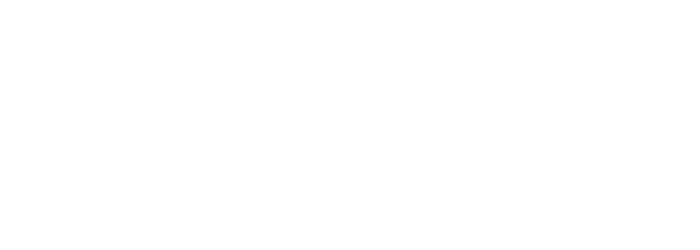
Rotation angle sensor (resolver) for EV/HEV electric motor
History of the resolver development over half a century
The history of resolver that MinebeaMitsumi produces is long, spanning half a century. We started with the development of synchro generators for aircraft instruments. Since then, we have accumulated know-how in resolvers through the development of products used in various applications such as those for industrial motors and automobile electric power steering motors. Since our entry into the automobile industry with the development of torque sensors for Toyota Zero Crown released in 2003, we have been supplying parts to major automobile manufacturers including Toyota, Renault-Nissan and Hyundai as well as other established motor manufacturers.
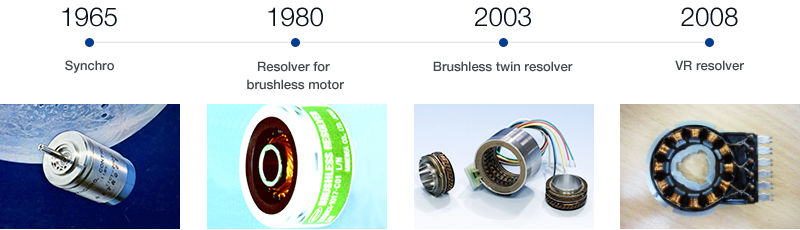
In 2012, we developed a VR resolver specifically for Nissan LEAF that is a next-generation eco-friendly car. Mobilizing our know-how cultivated over about half a century, we have succeeded in supplying highly reliable (heat resistance, oil resistance, etc.) and superior-quality products through our stable production system. There, various unique and proprietary technologies of MinebeaMitsumi are utilized.
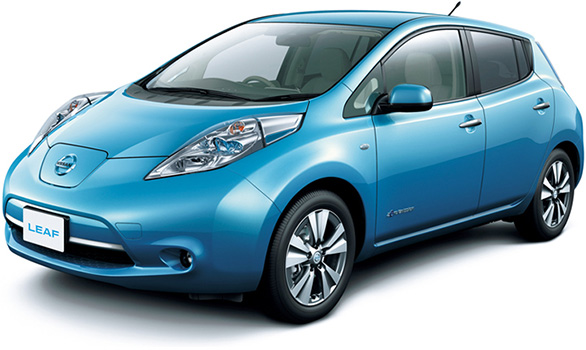
Nissan LEAF (photo by courtesy of Nissan Motor)
Organic combination of the technologies cultivated in the production of rotary components and machined components
Technologies cultivated in the production of rotary components and machined components are incorporated cross-sectionally in the revolver, ranging from the electromagnetic technology and winding technology to the stamping technology. We produce high-precision resolvers by combining multiple technologies that only a comprehensive precision equipment manufacturer can realize.
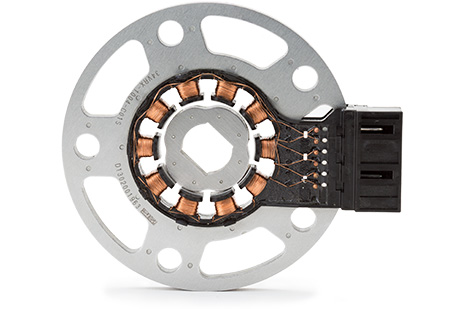
The speed of the motor that is the heart of the electric vehicle, Nissan LEAF, is controlled.
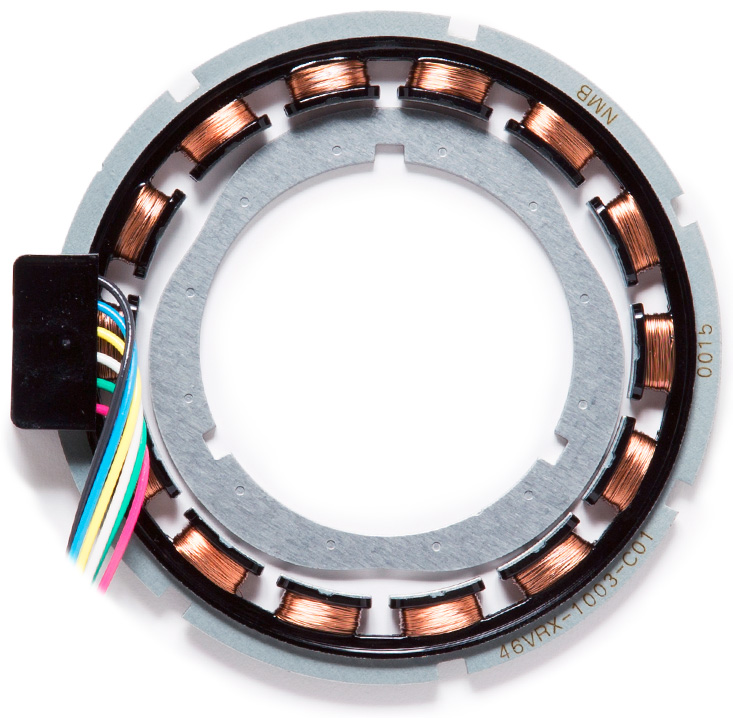
Winding technology that influences position detection accuracy
One of the parts that greatly influence the accuracy of a resolver is the winding provided in a stator. The angle is detected by means of an electric signal generated due to the change in reactance of the rotating rotor and fixed stator. A stable characteristic is maintained by making the winding even. New VR resolvers of MinebeaMitsumi are precisely adjusted at the design stage to achieve higher accuracy. In addition, to improve resolver performances and realize its mass production, the copper wire it contains must be wound fast and evenly.
MinebeaMitsumi's know-how in the motor production is utilized here. We applied our expertise in winding technology obtained through the motor production to the resolver, and this has made it possible to have faster copper wire winding than ever before. Furthermore, we designed in-house unique nozzles that are based on the diameter of the copper wire, and such nozzles are used for passing the copper wire. This allowed copper wire winding to be tight, highly accurate and stable.
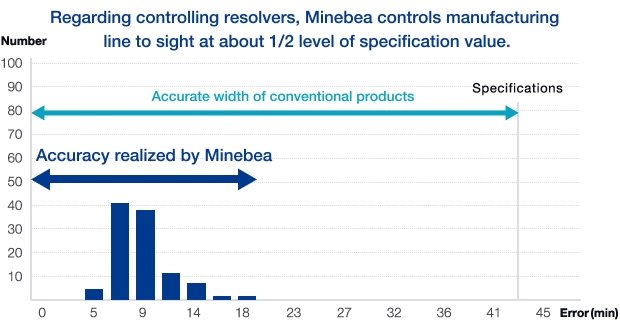
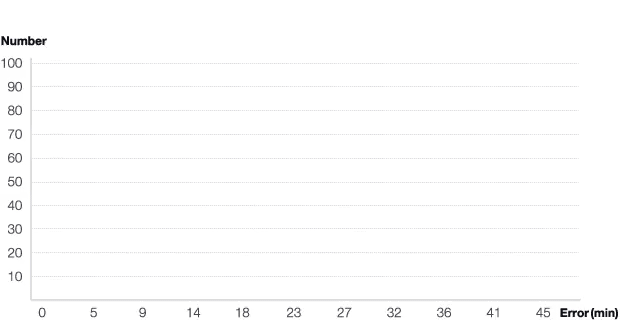
Accuracy of MinebeaMitsumi's winding technology
Welding technology for realizing high durability
The resolver that is directly connected to the motor requires not only high precision but also superior durability. In developing the VR resolver, MinebeaMitsumi focused on the connection between the copper wire and terminal. To enhance durability, we adopted TIG (Tungsten Inert Gas) welding instead of regular soldering. And to securely connect them, we melt the upper part of the wire-wound terminal to make a ball shape and enfold the wire with the melted ball. This method is also advantageous since welding quality can be easily controlled by visually checking the ball shape. Defects can be easily found if the ball is bent or collapsed. To accomplish this successfully, peeling of the copper wire coating and welding must be done simultaneously, and this requires an advanced technology. We have realized highly difficult TIG welding and kept superior durability and quality by applying our equipment condition setting technology that is one of the pillars supporting MinebeaMitsumi.
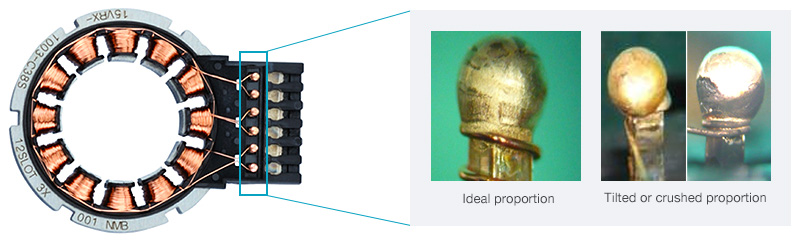
Product evaluation for maintaining high quality
We use our in-house ATF (Automatic Transmission Fluid) oil tester for inspection in the production process. It thoroughly clarifies the resolver life and the risk of deterioration in the performance of transmission oil. Thus, we realize high-level of quality control from the development to the production processes.
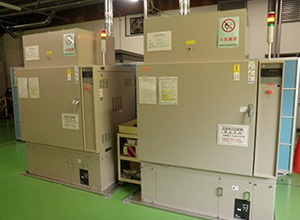
ATF oil tester
Stable parts supply by in-house production
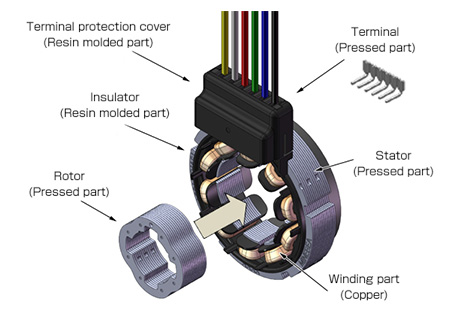
Many parts used in this product are made in-house by MinebeaMitsumi. For parts production as well, our resin forming technology cultivated in the manufacture of motors and our precision stamping technology accumulated in machine processing are applied. Parts that have been difficult to produce by conventional stamping technology can also be efficiently made by applying MinebeaMitsumi's precision stamping technology.
Besides the realization of efficient in-house production, we built a special production line for VR resolvers in our main production base, the Bang Pa-in Plant in Thailand, aiming to establish a mass production system for improving quality and supporting any sudden changes in demand. MinebeaMitsumi's stable supply system achieved by globalization is also one of its advantages.
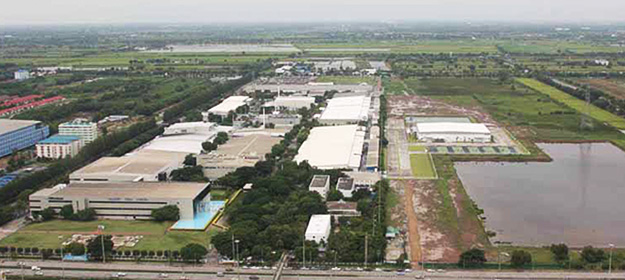
Bang Pa-in Plant, Thailand.
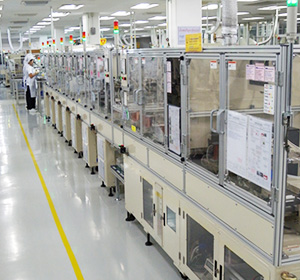
Production line for VR Resolvers in Bang Pa-in Plant, Thailand.
Basically, a resolver consists of a stator (input coil, output coil) and a rotor. Its structure is simple, but that is what makes it special. Its performance is greatly affected by the quality of its individual parts and the winding method of the copper wire. Originally, synchro generators, the prototype of a resolver, were mostly used for special applications in the aircraft industry and industrial machinery manufacturers. In recent years, however, resolvers have been playing an important role in automobiles that are very familiar products in our daily life. It is generally said that an aircraft synchro generator was originally developed in Western countries. However, the automobile resolver was first commercialized in Japan. It is precisely because we at MinebeaMitsumi have a commitment to ultra-precision technologies that we can produce sensors where the highest accuracy is required. We will keep supporting the development of the world's automobile industry by providing VR resolvers for EVs and other vehicles in small to large sizes that satisfy customer demand.
-
Detailed product information
You can view detailed product information here.
-
Contact
Please contact the below.
Other Columns
It ends about main text.