Relationships with Customers Back Number (2016)

Back to Latest Relationships with Customers
Basic Approach
The Minebea Group aims to be a comprehensive manufacturer of precision components which can make contributions to the development of global society. To this end, we practice the Minebea Group Quality Policy, which is based on the company credo the "Five Principles," to ensure the quality of products we develop, manufacture, and sell and thereby earn the trust of customers worldwide. Additionally, we use limited resources efficiently to prevent waste.
In support of our goals, we establish and operate quality management systems, while continually verifying their effectiveness and seeking ways to improve them.
Quality Management
Quality Management Framework
We have created a Quality Management Manual covering the entire Minebea Group as part of our measures to ensure the safety of our products and services and prevent accidents. The chief quality management system officer is the President and Chief Executive Officer, who is supported by the Quality Management Committee as well as its subordinate organization, the Group Quality Assurance Managers Meeting, which comprises managers responsible for quality in each business unit. These organizations regularly share information on specific quality issues and work to implement internal measures to ensure similar problems do not reoccur. The Group Quality Management Department acts as the administrative office for the Quality Management Committee and the Group Quality Assurance Managers Meeting, and provides quality management support and guidance to each business unit.
Established in FY2013, the Group Safety Regulation Council ensures compliance with the Electrical Appliance and Material Safety Law (in Japan), shares and promotes information on safety standards in each area of the world, and works to strengthen the Group's safety response.
Quality Management Framework
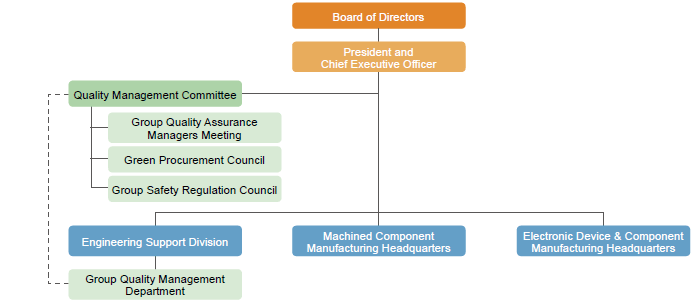
* The Group Quality Assurance Managers Meeting, Green Procurement Council, and Group Safety Regulation Council are comprised of representatives selected from the Manufacturing Headquarters and each business unit. Additionally, the Group Quality Management Department serves as the administrative office for the Quality Management Committee and its sub-organizations listed above.
Risk Assessment
Based on its internal standards, the Minebea Group conducts risk assessments on medical, automotive, and aircraft products—three types of end-products in which the Minebea Group's parts are commonly used and which could pose a serious impact on society in the event of a problem. These risk assessments are carried out collaboratively between the Group Quality Management Department and the business units. In the event the organizations identify a risk in design or manufacturing, actions are taken to mitigate the risk.
Quality Improvement Measures
Quality Assurance Agreement for Suppliers
In addition to basic contracts with its suppliers, the Minebea Group concludes quality assurance agreements to ensure that its entire supply chain can meet customers' quality standards. Regarding the manufacture of automotive parts, which present particularly high risks, we distribute quality manuals (quality requirements and specifications documents) and take other measures to ensure the highest levels of quality. In addition to automotive parts, the quality assurance agreement will also be gradually promoted among manufacturers of medical, aircraft and other parts posing a high risk.
Promoting Quality Management System Certification
The Minebea Group acquires quality management system (QMS) certifications necessary at each business site. We are also acquiring certifications in conjunction with the development of new products. Additionally, the Group Quality Management Department holds internal auditor training to continually nurture internal auditors and maintain its auditing capabilities.
Moving forward, each site will take preparations for transitioning to the latest ISO 9001 standard revised in September 2015.
Quality Management and Quality Control Examination
The Minebea Group promotes employees' acquisition of quality certification through quality control examinations (QC certification) administered by the Japanese Standards Organization and Union of Japanese Scientists and Engineers since September 2008. The certification improves each employee's quality assessment and management abilities, which leads to the improvement of higher product quality for the entire Minebea Group. In addition to covering employees' examination fees, we have created a database to share course materials as a way to raise quality management awareness, while providing seminars twice a year prior to examinations. In FY2015, many employees received certification, bringing the cumulative certification total for the entire Minebea Group to 548 employees (includes only employees currently employed by the Group).
Acquiring AEO Certification
The Minebea Group is strengthening and improving logistics management in order to perform trade and logistics properly and efficiently. As part of this effort, we are working to acquire Authorized Economic Operator (AEO) certifications. We applied for Malaysian certification in FY2015 and plan to acquire it in FY2016. We also plan to acquire certification in South Korea.
Unified Manufacturing Labels and Bar Codes
Among our logistics management activities, we are unifying manufacturing labels and bar codes throughout the Group to prevent mistaken product shipments and raise the productivity of verification processes. In FY2013, we began operating a system for domestically manufactured products, and in FY2014, we began promoting the system outside Japan. In FY2015, we began using the system for Thai-manufactured rod end products. We will continue to make preparations to expand this initiative to all of our manufactured products.
Disclosure of Product-related Information
Most products from the Minebea Group are ultimately integrated into finished products that pass into consumers' hands. For this reason, we provide safety related information to our customers as requested. Also in response to customer requests, we provide information about chemical substances incorporated in our products, based on information obtained from suppliers.
Communication with Customers
Customer Satisfaction Surveys
Within the Minebea Group, individual business units conduct their own customer satisfaction surveys. The survey results are provided to the sales and development departments of each business unit. If customers should evaluate any criterion below a specific satisfaction level, we assess and implement improvements across all divisions.
Responding to Quality-related Issues
In the event there is a major quality issue concerning Minebea Group products or services, we refer to our Quality Management Rules to take necessary measures in response.
Future Issues and Goals
Moving forward, we will strengthen our measures to further improve quality. Specifically, we plan to implement risk assessments and take measures to transition to ISO 9001:2015.
For logistics operations, we are strengthening management by unifying labels and bar codes for overseas manufactured products and promoting acquisition of certification.