Relationships with Customers Back Number (2013)
Back to Latest Relationships with Customers
Basic Approach
In accordance with the Minebea Quality Policy, the Minebea Group aims to fully satisfy customers in terms of quality, cost, supply capacity, and speed, working diligently to enhance its reputation as the most reliable component manufacturer.
As part of this effort, we place great emphasis on risk assessment at the product and process design stages, enabling us to provide our customers with products of consistently high quality.
Quality Management
Quality Management Framework
We have created a Quality Management Manual covering the entire Minebea Group as part of our measures to ensure the safety of our products and services and prevent accidents. The chief quality management system officer is the President & CEO, who is supported by the Quality Management Committee, an advisory body which assists in monitoring the performance of each manufacturing headquarters.
In FY2012, we revised the Quality Management Manual by adding new guidelines for improving product safety and bolstering the quality management structure. The Quality Management Support Office acts as the administrative organization for the Quality Management Committee. The office's responsibilities include providing guidance to business units and headquarters on ways to improve their quality management systems, quality assurance and research, and responding to major quality issues. In April 2013, we established the Group Quality Management Department as a replacement for the Quality Management Support Office to bolster the quality management structure and further improve our quality.
Quality Management Framework
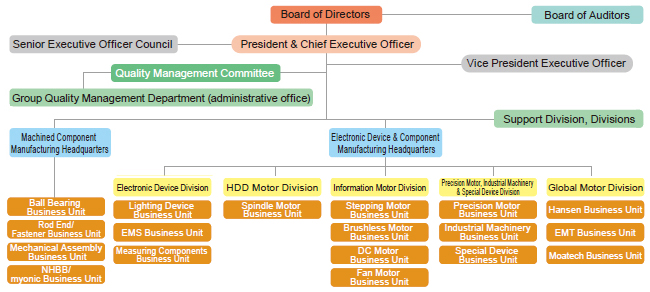
Quality Improvement Measures
Promoting Quality Management System Certification
The Minebea Group promotes the acquisition of certification for quality management systems (QMS) in each business unit. In FY2012, the DC Brush Motor Division acquired QMS (ISO9001) certification at the Cambodia Plant, which began production in FY2011.
Responding to the Quality Control Examination
The Minebea Group believes that improving the quality control and quality enhancement ability of individual employees ultimately leads to improving the quality of the Minebea Group. Since September 2008, we have been encouraging employees to sit for the quality control examination (QC examination) conducted by the Japanese Standards Association (JSA) and Union of Japanese Scientists and Engineers (JUSE). In addition to covering employees' course fees, we distribute textbooks and provide preparatory seminars to improve their knowledge of quality management. There were 82 employees who sat for the examination in FY2012, 73 of whom passed. A total of 377 Minebea Group employees have passed the examination so far.
Quality Management Team in Thailand
QMT in action
In Thailand, the Minebea Group has organized a Quality Management Team (QMT) comprised of representatives from the local business units. The team strives towards continual quality improvement by supporting the improvement of the quality systems and specific quality problems of multiple divisions in Thailand. QMT spends two-to-three months engaged with a single manufacturing division pursuing collaborative improvement activities with the division's own quality team.
The QMT also leads training and brainstorming sessions on quality approaches and practical application in order to raise employee motivation towards continual improvement.
Acquiring AEO Certification
The Minebea Group is strengthening and improving logistics management in order to perform trade and logistics properly and efficiently. As part of this effort, in November 2012 we received AEO system (STP-Plus: Secure Trade Partnership-Plus) certification from Singapore Customs. Our FY2012 goals also included preparations for AEO certification in South Korea and EU. After further study, certification preparation was suspended in these regions.
Unified Manufacturing Labels and Bar Codes
Among our logistics management activities, we are unifying manufacturing labels and bar codes throughout the Group to prevent mistaken product shipments and raise the productivity of verification processes. For bearings products, our global sales companies are required to use bar coding systems at warehouses to check product models and specifications when products are shipped into and out of the warehouses. For other types of products as well, we are making preparations to unify the manufacturing labels and bar codes.
Disclosure of Product-related Information
Most products from the Minebea Group are ultimately integrated into finished products that pass into consumers' hands. For this reason, we provide safety related information to our customers as requested. Also in response to customer requests, we provide information about chemical substances incorporated in our products, based on information obtained from suppliers.
For speakers, keyboards and some other finished products, user manuals include safety-related information.
Communication with Customers
Customer Satisfaction Surveys
Within the Minebea Group, individual business units conduct their own customer satisfaction surveys. This research spans a comprehensive range of evaluation criteria, including sales support, response to product related problems, and product prices. Findings based on these data are fed back to the sales and development division of the corresponding business units. If customers should evaluate any criterion below a specific satisfaction level, we assess and implement improvements across all divisions.
Responding to Quality-related Issues
In the event that there is a major quality issue concerning Minebea Group products or services, we refer to our Quality Management Manual and take necessary measures in response.
In FY2012, we held briefings for all business units in conjunction with the revision of the Quality Management Manual. The briefings explained detailed rules on internal Group procedures issued in FY2011 for dealing with major quality issues as well as recall guidelines for keyboards and other products sold directly to consumers. The 43 participants to the briefings are taking responsibility for raising awareness of the briefing contents among colleagues in their business units.
Future Issues and Goals
Moving forward, we plan to bolster efforts to improve quality under the new promotion structure. Specifically, we plan to create frameworks to compile and analyze the results of risk assessments conducted for each of our major products, while formulating new product safety guidelines.
In the area of logistics, we will make progress unifying the manufacturing labels and bar codes for all of our products.